CRAFTSMANSHIP
Special Projects offers the full spectrum of services representing total-project management and creation: from conception and design to final paint and assembly. We’re one of the only companies in the world that handles each process in house, providing award-winning work in an exceptionally secure and confidential environment.
Our success comes from taking a sensible approach to our work. We won’t use a five-axis mill when a skilled craftsman with a small knife will work just as well. We simply use the level of technology best suited to the job at hand. When high technology is the right choice, we use it well. It’s our ability to be versatile and agile that ensures we finish projects on time and on budget—without sacrificing creativity and quality.
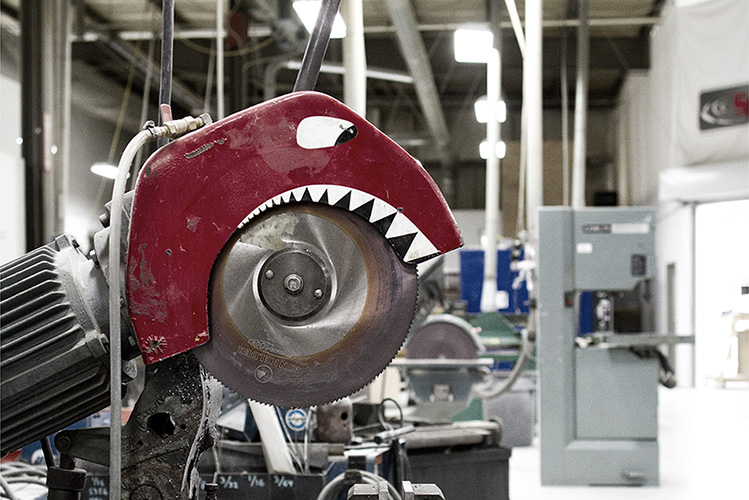
SELECT THE CAPABILITY YOU WOULD LIKE TO VIEW
EQUIPMENT
- Acurshear (10' X 1/4” capacity)
- Acurshear brake press (10' X 1/4” capacity)
- 2 Bridgeport vertical milling machines
- 12” diameter capacity machine lathe
- Do-all band saws vertical and horizontal
- Miller tig and mig welders
- Wisconsin Oven 6’ H x 6’W x 8’ L up to 500 degrees for post curing and thermo-forming
- 1 million BTU heated spray booth 16’ x 28’
- 16’ x 24’ paint/primer booth
- Formac brand thermo-forming machine
- Four precision vehicle build surface plates
- Hexagon brand optical surface scanner
- 5 precision CNC milling machines
- Various metal shaping equipment
- Tarus 5 axis linear motor drive mill 28’X x 6’Y x 9’ Z
- 2 Hass 3 axis 5’ x10’ x 2’
- 1 Hass 3 axis 7’ x 12’ x 2’
- Quasar 3 axis 36” x 72” x 16”